Air conditioning ducts are used in air conditioning systems to transport cool air from an appliance
Air conditioning to the space to be conditioned, or transferring air from the space to an exhaust fan
Exhust in case of ventilation or……etc
duct : –
– (S.A.D) supply air duct
– (R.A.D) Return air duct
– (F.A.D) Fresh air duct
– (Ex.A.D) Exhust air duct
✓ Another classification of Duct -:
– Galvanized steel
– Stainless steel
– Aluminum cladding
Galvanized Steel Ducted from galvanized sheet
-It is the most common type
– Galvanized sheet is rust and fire resistant
– Galvanized sheet duct can be manufactured in the form of
(rectangular – circular – oval)
The rectangular duct is the most widely used for the following reasons:
A- Ease of formation and control over its dimensions (especially height).
B- Reducing the wastage of sheet metal
C – manufacturing licenses compared to the circular duct
Stainless Steel Duct
• It is often manufactured in a circular shape
• Resistant to rust, fire and bacteria growth
• It has special applications such as the hygienic application
(Operating rooms) Medical application
Textile ( Fabric ) Duct
It is used only as a supply air duct.
The air is distributed along the length of the duct, and there are no air outlets installed on it.
It is easy to install, lighter in weight, and cheaper with lower noise levels compared to other types. However, its disadvantages are that it is not fire-resistant, and it is manufactured by specialized companies.
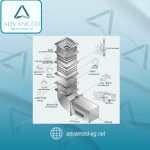
Design (Sizing):
There are several factors to consider when designing:
1- False ceiling height:
The height above the suspended ceiling must be known from the architect, meaning how much space is available above the false ceiling so that the available space is not insufficient, for example, if the available space is only 40 cm, and I design the duct height to be 45 cm.
2- Aspect ratio:
This is the ratio between the width and depth of the duct. The aspect ratio should be 𝑤𝐻 ≤ (1:4), and the closer the ratio is to 1:1, the better the performance and cost.
3- Air velocity:
The air velocity inside the duct should be appropriate. If the velocity increases, the duct dimensions decrease, but the noise level increases. If the velocity decreases, the noise level decreases, but the dimensions of the duct increase, and the cost is higher. There are tables in the SMACNA code that determine the recommended velocity for different applications. For example, for a studio, it is 350-500 feet/min, for residential areas, it is 650 feet/min, for operating rooms, it is 900 feet/min, and for factories, it is 1200 feet/min.
4- Size of air outlet:
The dimensions of the branch duct should be proportional to the dimensions of the air outlet. For example, if the air outlet dimensions are 16×16 inches, the branch duct width should be at least 2 inches wider.
5- The length of the duct should be as short as possible. The AHU or FCU should be as close as possible to the space to be air-conditioned, depending on the architectural design, and the noise level should be considered. The number of bends and connections in the duct should be reduced to minimize pressure drop and cost.
6- It is not necessary to change the duct dimensions after each branching. If the change in dimensions is less than 2 inches, there is no need to change them.
7- When changing dimensions, it is preferable to fix one dimension and change the other (preferably fix the depth) as this is better for manufacturing, installation, and reducing waste.
There are several methods for designing the duct, including:
1- Equal Friction Method
2- Equal Velocity Method
3- Static Regain Method
The Equal Friction Method is the most commonly used method. The method relies on constant pressure loss values in inches of water per 100 feet of duct length for the main and branch ducts. The velocity decreases as the air flow rate (CFM) decreases, and the maximum allowable air velocity is determined by the code tables according to the application.
The recommended pressure loss values are:
– For supply air duct: Δp = 0.08″ w.g / 100 ft
– For return air duct: Δp = 0.06″ w.g / 100 ft
– For fresh/exhaust/smoke duct: Δp = 0.1″ w.g / 100 ft
The duct design can be done using software such as Duct Sizer, Duct Mate, Duct lator, Friction losses/airflow chart.